Revealing the Art of Light Weight Aluminum Casting: A Comprehensive Guide for Beginners
In the realm of metalworking, aluminum casting stands as a craft that marries creativity with precision. Understanding the subtleties of this old strategy can be both rewarding and intriguing, especially for those venturing into the globe of casting for the very first time. As novices begin on this journey, they are encountered with a labyrinth of methods, devices, and security methods that form the foundation of mastering the art of light weight aluminum casting. This thorough overview intends to debunk the procedure, supplying a roadmap that browses through the history, fundamentals, steps, precautions, and alloys vital for those seeking to create their very own light weight aluminum castings.
History of Aluminum Casting
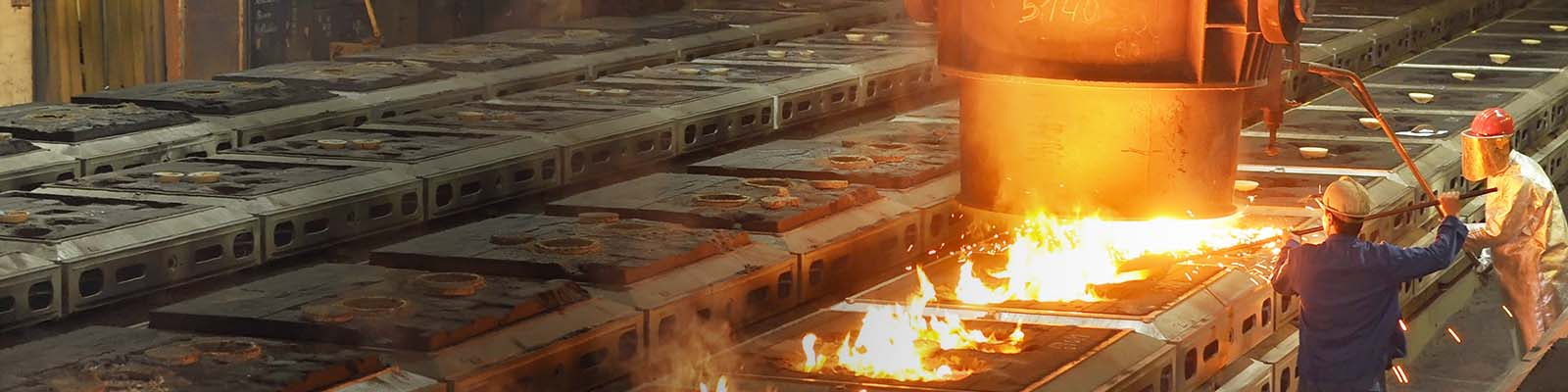
One of the essential turning points in the history of light weight aluminum spreading was the invention of the first light weight aluminum casting maker in 1886 by Charles Martin Hall. This advancement reinvented the market by enabling for automation of light weight aluminum spreadings, paving the way for its prevalent usage in numerous industries such as automobile, aerospace, and construction. Over the years, advancements in innovation have even more improved the light weight aluminum casting process, making it much more exact, economical, and eco-friendly. Today, aluminum spreading remains to play a vital role in the production market, using a versatile remedy for creating intricate components with high strength and resilience.
Essential Devices for Beginners
When getting started on the journey of aluminum casting as a newbie, acquiring the necessary devices is paramount for ensuring a smooth and successful spreading procedure. A crucible, commonly made from graphite or clay-graphite, is basic for thawing light weight aluminum. Crucible tongs are required for taking care of the warm crucible safely. A furnace, either gas-powered or electric, is crucial for melting the aluminum to its fluid state. To remove pollutants and solidified bits, a skimming device is essential. A stirring pole assists in making certain and blending the liquified light weight aluminum uniformity. Flask and molding sand are essential for creating molds into which the molten light weight aluminum is put. A mold and mildew frame, consisting of drag and deal, is needed for molding the sand. Airing vent poles aid in producing channels for air and gas to leave from the mold during casting. Safety tools such as heat-resistant handwear covers, apron, and face guard are crucial for securing oneself throughout the spreading process. With these vital devices in hand, newbies can start their aluminum casting trip with self-confidence.
Basic Actions in Aluminum Spreading
To launch the aluminum casting procedure efficiently, novices must first prepare the mold and mildew and guarantee its proper alignment within the mold framework - aluminum casting illinois. It is necessary to allow the aluminum adequate time to cool and strengthen inside the mold and mildew prior to trying to remove the spreading.
After the aluminum has cooled down and solidified, the mold needs to be open up to reveal the freshly developed spreading. Novices must wage care throughout this action to avoid damaging the mold and mildew or the spreading. The excess product, known as the sprue and any additional imperfections, can be removed by trimming and sanding the casting. The spreading can be brightened and ended up according to the wanted requirements. Grasping these standard steps is essential for novices looking to explore the art of aluminum casting.
Common Types of Light Weight Aluminum Alloys
Among the vital factors to consider in aluminum casting is understanding the varied variety of light weight aluminum alloys typically utilized at the same time. Aluminum alloys are classified based on read this their chemical make-up and homes, with each kind offering distinct qualities fit for different spreading applications. One typical aluminum alloy is A356, recognized for its exceptional castability and excellent mechanical buildings, making it prominent in numerous sectors such as automotive and aerospace. Another widely utilized alloy is 6061, valued for its high strength and corrosion resistance, making it ideal for structural elements and marine applications. Additionally, the 380 alloy is favored for its superior fluidness and machinability, making it a top selection for elaborate spreadings calling for complex details. Comprehending the properties and advantages of these typical light weight aluminum alloys is essential for newbie casters to select the most ideal alloy for their certain casting needs, making certain quality results in their spreading projects - aluminum casting illinois.
Safety And Security Preventative Measures in Casting Aluminum
Thinking about the vital function of aluminum alloys in the spreading procedure, focusing on safety preventative measures is vital to make certain a safe and secure and reliable casting atmosphere. When collaborating with liquified aluminum, it is important to wear ideal individual protective tools (PPE) my blog such as heat-resistant gloves, aprons, encounter guards, and safety and security goggles to avoid burns and injuries. In addition, ensure correct ventilation in the casting location to minimize direct exposure to damaging fumes and gases launched throughout the melting procedure.
To avoid potential fires, constantly have a fire extinguisher nearby and develop a clear emptying plan in situation of emergency situations. It is important to carry out normal safety training sessions for all employees involved in the casting operation to inform them on ideal methods and emergency situation treatments. Proper handling of tools, including crucibles, ladles, and molds, is important to avoid crashes and maintain a safe workplace.
Furthermore, preserving a tidy and organized work space can help in reducing the risk of slides, trips, and drops. By adhering to these safety and security precautions, newbies can create a protected structure for understanding the art of aluminum casting.
Verdict
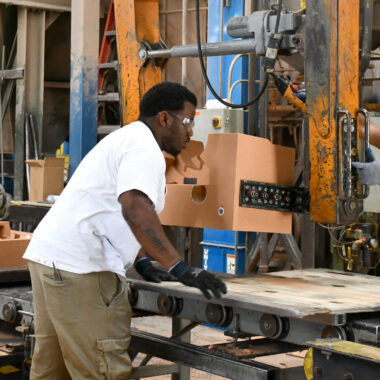
It was not up until the 19th century that significant advancements in light weight aluminum spreading were made, particularly with the advancement of more efficient approaches for melting and forming aluminum alloys.
One of the crucial landmarks in the background of light weight aluminum casting was the development of the very first light weight aluminum spreading machine in 1886 by Charles Martin Hall.When beginning on the journey of aluminum casting as my review here a beginner, obtaining the vital devices is critical for making certain a smooth and effective casting procedure.One of the essential factors to consider in aluminum spreading is recognizing the varied range of aluminum alloys typically made use of in the process. By understanding the crucial devices and standard steps entailed in light weight aluminum casting, beginners can efficiently work with different types of light weight aluminum alloys.
Comments on “Raise Your Tasks with Aluminum Casting Illinois: Let's Collaborate”